If you're intrigued by the style and economy of manufactured housing but have wondered just how mobile homes are built, the mobile home manufacturing process has become streamlined and efficient since they were first introduced as a solution to the need for low-cost housing.
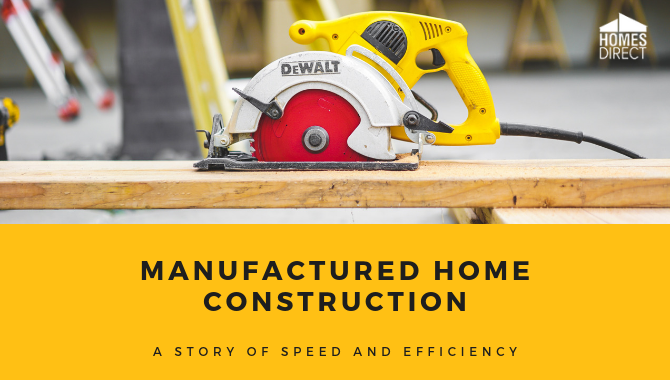
Mobile, Modular, Manufactured. What’s different?
The terms are related, but there are distinct differences. The term "mobile home" is used to refer to what used to be known as "trailers," typically small, inexpensive homes that were on wheels and could be moved from one site to another without a lot of trouble. They were built in great numbers in the years following World War II because they could be produced quickly to meet a real need for affordable housing. Their construction was largely unregulated.
Manufactured homes today (often called mobile) are highly regulated, and although they may arrive at their permanent sites with wheels still attached, the wheels are typically removed and the homes are attached permanently to an in-ground foundation. They may consist of a single module, or two or more can be joined together to form a larger house. With skirting and landscaping, they are virtually indistinguishable from site-built homes. Structuring and building a mobile home is a very interesting process.
Modular construction is just what it sounds like. Factory-built modules that may be single rooms can be combined in many ways at a physical site. They might be stacked or joined in sequence to serve as offices, retail spaces, hotel and motel rooms, and schools as well as homes. Size limitations exist only in terms of transporting modules to a permanent site.
Park Homes are a newer "invention," with many of the same advantages of both recreational vehicles and mobile homes. They are limited in size to 400 square feet, are built in the same factories and to similar standards as manufactured housing, but are designed to be semi-permanent "cabins" or recreational housing, placed in camping areas or "trailer parks," but tied to existing utilities to provide home-like comfort. Park home manufacturing has become very common nowadays. It is a way to the modern approach of affordable living. Building a mobile home can be truly unique to you and your needs.
Read also: Mobile vs Manufactured vs Modular vs Park Homes
Mobile Home Construction Diagram
Manufactured Home Construction Process Overview
#1: All Starts with a Foundation
Understanding how manufactured homes are built can help you remodel or modify a home. This is especially true when you have to replace the flooring or move walls in a mobile home. Knowing the construction methods that are involved, what are mobile home walls made of and the order of construction, can help you plan your project better and save money. Just like everything else, building a mobile home has improved and has become much better.
Let’s start from the beginning of building a manufactured home. Every good home needs a strong foundation, and manufactured homes are no exception. Mobile home construction begins with an engineered steel I-beam frame designed to carry the weight of the finished structure. Once the frame is welded together and stabilized, it may be topped with decking and a thin layer of concrete. The foundation is then ready to carry the weight of the wall framing and the roof and ready for interior plumbing, fixtures, cabinets, and appliances.
Mobile home framing would be one of the priorities in the process. Understanding every step and implementing the right procedure can be crucial. If you are thinking about buying a mobile home, start finding a mobile home frame to your taste.
The foundation must be strong enough to support not only the weight of the finished structure but must also withstand the stresses of transportation to a permanent location.
#2: Floor, Walls, and Roof
As it is said, mobile home construction details always matter. While constructing a mobile home it is very essential to be detail-oriented when it comes to the walls, roof, or the floor specifically. Typically, a manufactured home facility utilizes a number of different "stations," all within a compartmentalized factory setting, to construct the various components of a finished home. Skilled laborers measure and cut wood and finishing materials to the exact sizes called for on the plans. Walls, roof sections and other parts of the home are built in modules that can be easily tied together as they are needed. Walls are placed where they belong on the foundation and screwed together. Other workers run electrical wires and plumbing lines, add necessary insulation and drywall, sheathing and sealants, and in almost no time at all - a home can be finished. The mobile home structure which can differ of course, should be kept following the steps.
#3: Putting It All Together. Home Siding and Utility Hookups
The separate tasks of framing, cabinet construction and placement, plumbing, wiring, insulation, window, and door installation, and joinery are completed by specialized crews. Work on multiple parts of the building can proceed at the same time. The mobile home materials are not difficult to put together. Because the homes are built to precision plans, materials are typically cut to measure in advance and stockpiled at the factory until they are ready to be used, resulting in enormous savings in terms of time and cost. There is also a minimal amount of waste. In addition, because all the work is completed in a climate-controlled manufacturing plant, there is never a worry about weather delays.
One of the main reasons people chose mobile homes is the easy maintenance and less pricier option compared to site-built houses. Making a mobile home look like a house has also been one of the main steps on the way. In general, it's much easier to make a double-wide look like a regular house, but a single-wide is not impossible either. By adding mobile home exterior wall constructions and parts can make everything possible and close to your dream house.
#4: Code Compliance and Safety Standards Inspections
Since 1974, all mobile homes have been built to standards developed specifically for manufactured housing by the U.S. Department of Housing and Urban Development. Known as the HUD code, it is the only federally-mandated building code that exists. All manufactured homes must comply with stringent codes that address building safety and construction practices. In addition, third-party inspectors validate building procedures before the home is delivered. Each mobile home bears a permanent-affixed certification seal.
Wondering how long do mobile homes last? When installed properly, following mobile home insulation standards, a manufactured or modular home can last just as long as a regular home built directly on a construction site. Throughout the building process, quality is maintained not only by staff supervisors, but also by third-party inspectors, and any potential problems are immediately addressed. As the home nears completion, various tests are performed to ensure that all plumbing and electrical lines are working properly, that the entire building is code-compliant, and that specifications have been followed completely.
#5: Transportation, Setup, and Final Touches
When construction is complete, the manufactured home is transported to its site, where it may be slid or pushed into place, or lifted by crane onto its prepared site, either a reinforced pier-and-beam foundation, an excavated basement, or sturdy stem walls. The home is securely attached to ground anchors, and reinforced with steel straps to ensure long-term stability and prevent shifting from high wind and other forces of nature. Once the plumbing has been connected to on-site water and sewer lines, and the heating, cooling and electrical lines are completed, the home usually receives a final inspection and approval prior to being occupied by its new owners.
Read also: Manufactured Home Setup. A Comprehensive Guide to the Installation Process
Owning a Manufactured Home
Manufactured housing is appealing to buyers for many reasons. Prime reasons for looking at mobile home construction as an option include the variety of floor plans available, the speed at which a home can be completed, affordability, an ability to personalize both the interior and exterior styles, and the list of communities that either welcome mobile homes or consist entirely of manufactured housing.
Today's manufactured housing is safe, attractive, well-built and durable, and offers great value.
Homes Direct is available to answer all your questions about how are mobile homes built and help you on the path to home ownership.
FAQ
How are manufactured homes built?
Manufactured homes are completely constructed in a factory and then transported to the home site. Once they arrive at their destinations, they are indistinguishable from site-built homes. They are usually not moved again.
They are built according to federal construction codes from Housing and Urban Development (HUD).
Are mobile homes frame construction?
Mobile home construction begins with an engineered steel I-beam frame designed to carry the weight of the finished structure. Once the frame is welded together and stabilized, it may be topped with decking and a thin layer of concrete.
What are the walls of a manufactured home made of?
While not every mobile home is the same, there’s a good chance your walls are either drywall or VOG (vinyl over gypsum). Your mobile home may have walls made out of wood panels, and if so that probably means it’s quite old.
Are manufactured homes wood framed?
Usually manufactured homes are steel I-beam framed, designed to carry the weight of the finished structure.